The wide range of power speed regulation is a limitation of permanent magnet motors. Yueneng company learns from the experience of electric vehicle motor system, adopts the structure of permanent magnet-reluctance synchronous motor, which effectively breaks through this limitation and can fully meet the requirements of injection molding electromechanical servo applications.
The motor rotor position/speed sensor is used to control the torque and speed of the servo motor. It is necessary to detect the position and speed of the motor rotor. Most servo motors use photoelectric encoders as position/speed sensors. The advantage of the optical encoder disk is that the structure is simple and easy to obtain high accuracy, but because its processing circuit must be integrated with the motor, in the environment of high motor temperature and vibration, coupled with electromagnetic interference, its electronic circuits often cannot In normal operation, there is missing code, causing motor control disorders or even damage to the motor.
Yueneng servo system adopts a high-performance rotary transformer that meets the requirements of electric vehicles as a speed feedback component. It has a firm structure, high temperature resistance, vibration resistance, and strong anti-jamming capability, ensuring that the system works stably and reliably in the "nasty" environment of injection molding machines. And the precision can reach 4096 pulses per revolution.
Servo Drive Controller The servo drive controls the current, torque and speed of the servo motor according to the pressure and flow commands of the injection molding machine controller (upper computer). Yueneng servo drives include servo control, rectification/inverter power, communication interfaces, and feedback detection. The rectifier/inverter power unit uses advanced integrated IGBT modules; the servo control unit includes position controllers, speed controllers, torque and current controllers. A high-speed digital signal processor (DSP) is used as the control core of the driver to implement various complicated control algorithms, and a pulse width modulation (PWM) signal is output to an inverter power driving circuit to change the output power of the inverter to achieve control. The purpose of permanent magnet synchronous AC servo motor.
The oil pump serves as the main power source of the injection molding machine, and the good matching of the oil pump and the servo system is crucial to the performance and energy saving effect of the whole machine. The oil pumps that are currently used in servo systems include gear pumps, plunger pumps, and screw pumps, which have different characteristics. Therefore, the servo system must be able to adapt to various oil pumps and optimize parameter settings. Yueneng servo system has advanced load parameter identification function, which can flexibly optimize and adapt various oil pumps.
Pressure feedback component - pressure sensor Yuen servo system adopts pressure closed-loop control strategy, that is, by controlling the motor torque and speed to adjust the injection molding machine oil pressure and follow the pressure command value. The oil pressure signal is obtained by the pressure sensor, and its accuracy will determine the control precision of the injection molding machine pressure. Imperial can provide pressure sensors with different control accuracy requirements.
Field Oriented Control Technology The basic principle of field directional control (vector control) is to simulate the torque control law of a DC motor on a three-phase permanent magnet synchronous motor. In a magnetic field orientation coordinate, the current vector component is decomposed into excitation current components that generate magnetic flux. And generate a torque component of the torque current, and make the two components perpendicular to each other, independent of each other, and then adjust them separately. The vector control of the AC motor decouples the control of the torque and the magnetic flux, does not affect the magnetic flux when the torque is controlled, and does not affect the torque when the magnetic flux is controlled, making the AC motor control as convenient as the DC motor control. The dynamic characteristics comparable to DC speed control systems are available.
In order to maintain the maximum output torque of the motor, the system needs to obtain the instantaneous position and speed of the rotor of the motor. Through the coordinate transformation of the measurable stator variable, it is transformed into the rotor coordinate system to form a closed loop of current and dynamically track the current. Changes, and then use the speed sensor to form a closed loop speed, the ultimate realization of current and speed double closed loop, to obtain excellent system stability, rapid response and control accuracy. These complex operations require high-speed digital signal processing on the chip DSP.
Another advantage of field-oriented control is that, through the separate control of the torque current component and the flux current component, the copper loss and iron loss of the motor are optimally distributed, thereby obtaining the best system efficiency.
Electro-hydraulic servo system control principle and algorithm
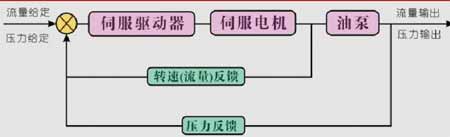
Fig. 2 Electrohydraulic servo control system block diagram
Combined with Figure 2 and the system structure, the system control principle is briefly described as follows: Immediately receive the flow and pressure reference signals from the main control board of the injection molding machine; instantly detect and feedback the pressure from the oil pump and the speed from the motor.
For the error between the given and the feedback, the high-speed DSP of the servo driver uses various control algorithms to generate the control signal for the servo motor and drives the servo motor through the IGBT module to realize the double closed-loop control of the pressure and the rotation speed. (To be continued)
Paper Display Board,Cardboard Display,Paper Display
Necklace Bust Display Co., Ltd. , http://www.nsjewelrytray.com