Commercial rotation Offset printing machine is often referred to as "commercial rotary machine" or "merchant ships." Different from sheetfed offset presses and other forms of rotation Printing machine, merchant ships taking into account the production speed, print quality and functionality, to ensure printing precision at high speeds. At the same time, it can complete a series of work such as double-sided printing, drying, folding, etc., and can expand additional functions such as connecting glue, connecting ridges, connecting cutting, etc., which can be widely used in large batches. Print production with short lead times, such as full-color magazines, promotional materials, direct mail, color newspapers, and yellow pages.
Market profile of the merchant ship
From the end of the 20th century to the beginning of the 21st century, it is a period of prosperity and development of China's commercial ship market. Many capitals are strong and strong. Book printing companies have purchased new importer wheels. At that time, China’s annual installed capacity of commercial vehicles was close to 10. After 2010, affected by the impact of electronic publishing and the overall shrinking of the book printing market, the new installed capacity of commercial ships fell sharply, but the domestic equipment holdings remained high, which also made the market increasingly fierce. In order for a printing company to gain a competitive advantage, it must start by reducing production losses, improving the stability of printing quality, and reducing the number of printing jobs for commercial wheels.
In addition to management methods, the application of automated auxiliary devices is an important way to help printing companies achieve the above requirements. The use of automatic color control system can not only greatly reduce the loss of the initial start-up of the equipment, but also maintain the stability of color and quality during the printing process. Loss, maintain print quality and reduce the number of prints. The systems associated with the automatic color control of the merchant wheel are mainly two parts of the CIP4 and the color control system of the printing press.
CIP4
If the color control system of the printing press is the "commander" of the printing color control, then CIP4 is the "pioneer" before the start of printing. Through CIP4, various information related to printing can be smoothly transmitted to various processes of the entire printing production process through JDF files, and information can be interconnected. In order to realize the color control of the merchant wheel through CIP4, the following requirements must be met.
First, the press and the prepress system must be connected to the same network. When the original is processed before printing, a JDF file is generated to store various types of data. Specifically include: basic information, such as job name, customer name, number of jobs and delivery deadline; printing machine preset data, such as Color separation preview image, ink preset data, ink fountain roller speed, water fountain roller speed, etc.; binding and processing data, such as cutting size, folding line position, number of posts, etc.
Second, it must be adopted CTP plate making. The CTP process is the key to CIP4's integration of prepress and printing, enabling the instruction set of JDF files to be sent directly to the press. At the same time as the CTP prints the plates, the ink amount information of each ink zone of each color group will be written into the JDF file.
Finally, before printing, the merchant operator needs to enter CIP4 integrated on the merchant wheel to call the JDF file of the corresponding job. After the JDF file is called, the ink preset information, folder data, etc. contained in the file will be downloaded to the central control system of the merchant wheel, and then the central control system issues an instruction to pre-adjust the opening and closing angle and folding of the ink button of the ink fountain. The pre-adjustment position of each machine such as the page machine ensures the smooth production of the work piece.
When the dealership is up and running, the equipment operator can focus more on monitoring the status of the equipment and the quality of the prints.
Printing machine color control system
1. From open loop to closed loop
Most of the early commercial vehicles used the open-loop color control system, that is, the operator repeatedly took the printed sheets during the printing process, and adjusted the ink supply of the printing machine by measuring or visually comparing with the standard proofs to achieve stable printing color. the goal of. The main disadvantages are: slow response, long adjustment time, large printing loss, and mainly rely on the skill level of the operator.
In order to solve the above problems, the closed-loop color control system came into being, and its working process was mainly based on automatic measurement and control of the computer system, which greatly reduced the influence of human factors. The main principle is: during the printing process, the measuring device continuously scans the color control strip on the substrate, and after the background calculation and comparison with the ink preset standard, the instructions for the ink amount adjustment of each color group and each ink area are given, and the printing control is performed. The table sends an adjustment signal to the printing ink fountain to adjust or correct the thickness of the ink layer to achieve the purpose of automatically adjusting the printing color without interruption. This process theoretically does not require manual participation, and the adjustment speed is fast and accurate.
2. Two color control modes of closed-loop color control system
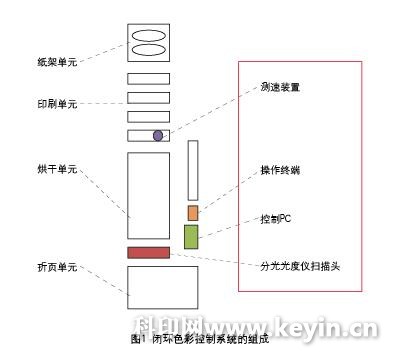
Sensor Sleep Mattress,Smart Monitors Mattress,Sleep Tracking Mattress,Sleep Tracker Smart Bed System
ZHONGYUAN INNOVATION CO.,LTD , https://www.yuvicoutdoor.com